For Webster University students, the recycling process is seen as far as the blue plastic bins that sit in hallways and classrooms around campus. The path the sought-after recyclables take after they leave campus reveals an intricate web of collection, processing, packaging and shipping.
Webster’s facilities operations department begins the recycling process when it collects the recyclables and puts them in yellow-lid containers.
Waste Management, Inc., Webster’s recycling and trash partner, then takes the university’s trash and single-stream recyclables to Rock-Tenn recycling facility located on Natural Bridge Avenue, said Angela Ingenthron, Waste Management’s public sector-education coordinator for the Missouri Valley area. She is also a Webster alumna who graduated in 1994.

“Waste Management’s goal with any university is to divert as much waste from the landfill and drive recycling as much as possible,” Ingenthron said.
Rock-Tenn Recycling is based in Norcross, Ga. In May 2011, Rock-Tenn bought out Smurfit-Stone Container Corp., a company based in St. Louis, for $4.9 billion. This made Rock-Tenn one of the largest manufacturers of recycling solutions and corrugated and consumer packaging. The company takes in more than $10 billion in revenue.
There are approximately 56,000 businesses involved in recycling and reusable materials. These businesses employ more than 1.1 million people, according to the U.S. Recycling Economic Information Study.
Rock-Tenn allows tours at its St. Louis recycling facility, but due to several restrictions, a tour was not possible for Journal reporters. However, a tour of the Republic Services recycling facility located at 4076 Bayless Ave. was provided. The tour allowed an up-close look at the single-stream recycling process.
Photos by Sean Funcik, audio by Elise Rich and video by Gabe Burns
Republic Services is a trash removal and single-stream recycling provider. It is the second-largest company, after Waste Management, Inc., for nonhazardous waste removal in the United States.
Jorge Pedraza, a shift supervisor at the south St. Louis Republic Services recycling facility, has worked for Republic for the past three years. He supervises sorting, packaging and single-stream recyclables. Pedraza provided the tour and explained the single-stream recycling process.
Walking through stacks of sorted commodities, Pedraza pointed out baled No. 1 through 7 plastics. Plastic containers are numbered to help consumers know what containers are recyclable. Each bale weighs approximately 1,000 pounds.
“Everybody wants the numbered 1 and 2 plastics, 1 plastics are like soda bottles and 2 plastics are like detergent bottles,” Pedraza said.
Plastic number 1 is polyethylene terephthalate, also known as PETE or PET. Plastic number 2 is high-density polyethylene, or HDPE.
Pedraza said the separation process starts as giant piles of single-stream recyclables are dropped off by Republic recycling dump trucks. Front loaders scoop the trash and dump it in a machine referred to as the drum feeder. The drum feeder “fluffs” up the products so when it gets to the sorters it’s not a huge lump, explained Pedraza. Conveyor belts then take the stream of recyclables to a second-floor assembly line of four workers, who grab out cardboard and trash so it does not jam up the machines.
“If you follow the product, you will end up dizzy,” Pedraza said.
Once the recyclables pass through the main sort line, they move to a machine with two metal screens that break up glass and let it fall to a pile. The conveyor then pushes the products — consisting mainly of plastics and paper — into a machine with fast-rotating paddles. The paddles push back the heavy plastics and allow the paper to move forward. As the recyclables are sorted, they fall to designated areas for each commodity. As the piles grow, front loaders pick up the sorted commodities and dump them in a baler. The baler crushes and binds the product so it is ready to ship.
Republic’s current recycling system is unable to sort aluminum cans. The aluminum cans often get mixed in with the plastics.
“We call it co-mingle,” Pedraza said.
Pedraza explained that the co-mingled bales are bought by a company in Minnesota that has technology to separate the product even further. Republic is currently investing $19 million to update its two recycling facilities in St. Louis, which would allow the company to sort out the aluminum cans themselves.
After the products have been baled, they are shipped by train or truck to paper mills, plastic plants and aluminum plants. The materials are sorted even further, sanitized and made into useable materials. Prices for the commodities vary depending on the market. The Official Board Markets: The Yellow Sheet (Chicago market) is a guide for the Midwest to determine the market value of commodities such as cardboard, standard office paper, single-stream recycling and several others.
“You hear about being green — recycle, reuse — but working here I really see that everything can be reused and remade,” said Pedraza. “People want the recycled commodities and will pay for them.”
Share this post

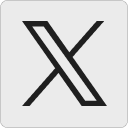



